Key Marks of Top Facility Care
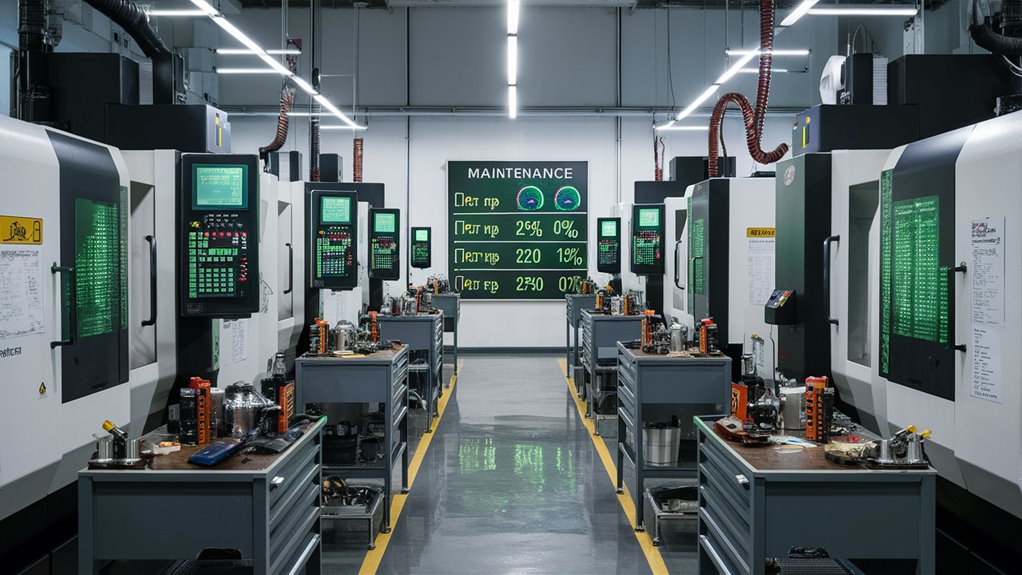
Top Signs of Well-cared Facilities
Good maintenance management shows through many clear signs that set great facilities apart from OK ones. Good gear, tidy spaces, and neat records are key signs of great care. These clear signs show a place’s pledge to good care plans and smooth working.
Key Care Scores and Rules
Care effectiveness is seen in a few key scores:
- Gear run times always above what others see
- Care that stops problems hits 90% or more
- Job done times hit or beat goals
- Gear trust scores show steady rise
Top Care Steps
Early care steps have clear traits that make them stand out from last-minute fixes:
- Detailed plans for when to do jobs
- Full life tracking of assets
- Smart tools that guess future breaks
- Well-thought-out stock plans
- Written out steps for doing tasks
Place Order and Safety Rules
Great maintenance shows in:
- 5S place order steps at work
- Clear safety steps in place
- Neat tool spots and gear storage
- Clean and tidy work spots
- New safety signs and right labels
Tech Use and Records
New care work uses:
- Digital care systems
- Online records of care steps
- Live watching tools
- Smart choices based on data
- Auto plans and work orders
Gear Run Scores: Get More Work Done
How to Get Gear Run Scores
Gear run scores show how well machines work, telling us how often and well they run when they should. These scores look at the percent of time tools work great during set work times, counting both mech readiness and work power.
Big Run Scores
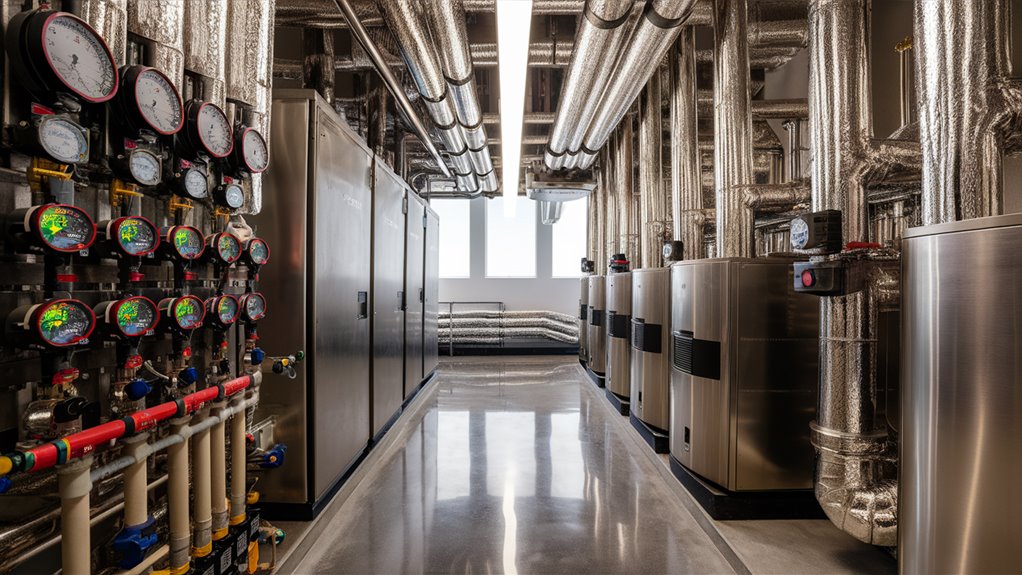
Avg. Time Between Stops (MTBF)
MTBF checks give useful hints on gear trust by finding the average span between breaks. This big score helps care teams guess and stop likely breaks, making gear last longer 베트남 가라오케
Avg. Time To Fix (MTTR)
MTTR reviews find out how fast care teams act, checking how quick they fix things. Short MTTR shows top care methods and better gear fixing steps.
Overall Gear Power (OEE)
OEE checks mix three main points:
- Ready Rate
- Work Power
- Good Output
Make Gear Work Better
Smart care steps are key to more run time:
- Set care times
- Full training for operators
- Digital gear logs
- Smart watch tools with auto alerts
- Find main causes for low scores
Getting better needs non-stop watch with auto tools that look for problems live. When scores drop, smart deep checks help make smart changes to care jobs, making gear trusty and less stops in work.
Job Answer Times
Job Answer Time Plans
Fast job time answers are key in up-to-date place care, changing gear trust, work smooth, and overall care.
Tracking Job Times and Scores
Job time watch needs steady eye from start to end. Top scores are:
- First answer time
- Fix done span
- Check again times
Priority-Based Answer Rules
Emergency Answer Steps
- Very needed fixes: Under 2-hour window
- Safety matters: Go right away
- Tool breaks: Quick check and start
Usual Care Times
- Regular care: 24-48 hour target
- Stop-problem work: Set by asset needs
- Not big fixes: Set in usual flow
Getting Better Methods
Better answer times rely on proven better ways:
- Color-tagged watch systems
- Online care software linking
- Live status watch
- Auto sending plans
Main Cause Reviews
Main slow points often come from known spots:
- Team training needs
- Parts ready issues
- Right record needs
- techniques that transform average
- Resource use hard spots
Often looking at these scores helps care teams get better answer times, less gear down time, and better tenant happy by making care better.